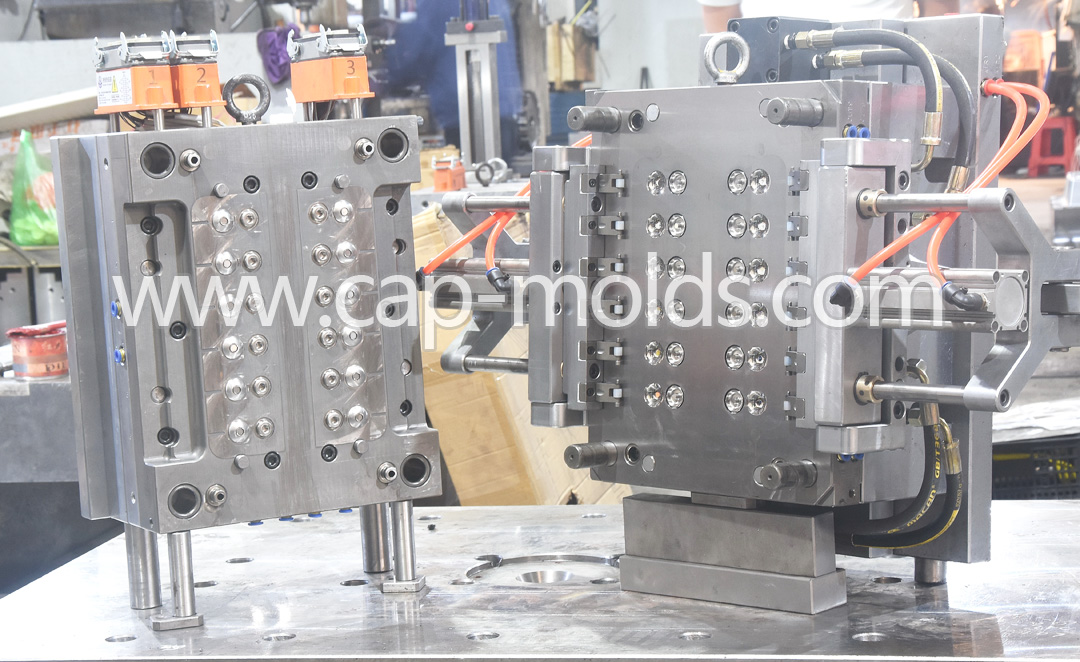
The advantages and design of bottle cap molds
Bottle cap moulds from 1 to 64 cavities are available: mineral water caps, beverage caps, five gallon caps, shampoo flip caps. All kinds of oil bottle easy-pull caps, sports caps, cosmetic caps, wine bottle caps and oil drum caps, etc.
The current application of plastic bottle cap molds is relatively extensive, suitable for multiple packaging industries such as edible oil, beverage, candy, medicine, etc., and has the characteristics of high quality, energy saving, high efficiency, and long service life.
The advantages of plastic bottle cap moulds:
1. Multi-cavity point. Plastic bottle cap molds have mature technology from 4 to 32 cavities, simplified hot runner work, and low cost.
2. High efficiency. The plastic bottle cap mold adopts a simplified dispensing hot runner, no glue mouth waste, and the cycle reaches 5 seconds.
3. High life expectancy. The cavity of the plastic bottle cap mold is made of high-quality mold steel, and the guide post and guide sleeve of the mold are lubricated without oil, which has the strong advantages of no pollution and a service life of up to ten million times.
4. The blade is specially designed. The unscrewing ring knife edge of the plastic bottle cap mold adopts a split structure, which can make the blade not deformed, the positioning is accurate, the replacement is easy, and the mold is closed without pressure. defect.
5. Plastic bottle cap molds have relatively complete and unified quality standards and caliber parameters, so the production of bottle caps is relatively standardized. It can be said that the plastic bottle cap mold determines the shape and quality of the product.
6. Each cavity of the plastic bottle cap mold is independently self-locking, which can ensure the concentricity of the mold, and the excellent cooling system can achieve high efficiency of normal temperature water cooling, and no need to cut the gate, which can reduce the labor intensity of workers.
Factors to consider when designing plastic bottle cap molds:
1. Number of cavities and placement method: bottle caps are mass-produced products as packaging containers, and a multi-cavity plastic bottle cap mold should be selected.
2. Pouring system planning: According to the layout of the plastic parts, the mold is designed as a three-plate type with point gates, and the gates are set at the center of the top of the plastic parts. The point gate can significantly increase the shear rate of the melt and increase the viscosity of the melt. In order to descend, it is conducive to filling the mold. Moreover, as a packaging container, plastic parts have high requirements for appearance quality, and the residual traces of the point gate are small, which can ensure the surface quality of the plastic parts; when demoulding, the gate is automatically broken, which is convenient to complete the automation of the product production process and improve production. power, increasing economic efficiency.
3. Cooling system planning: The mold temperature adjustment system of the plastic bottle cap mold directly affects the quality and production efficiency of the product.