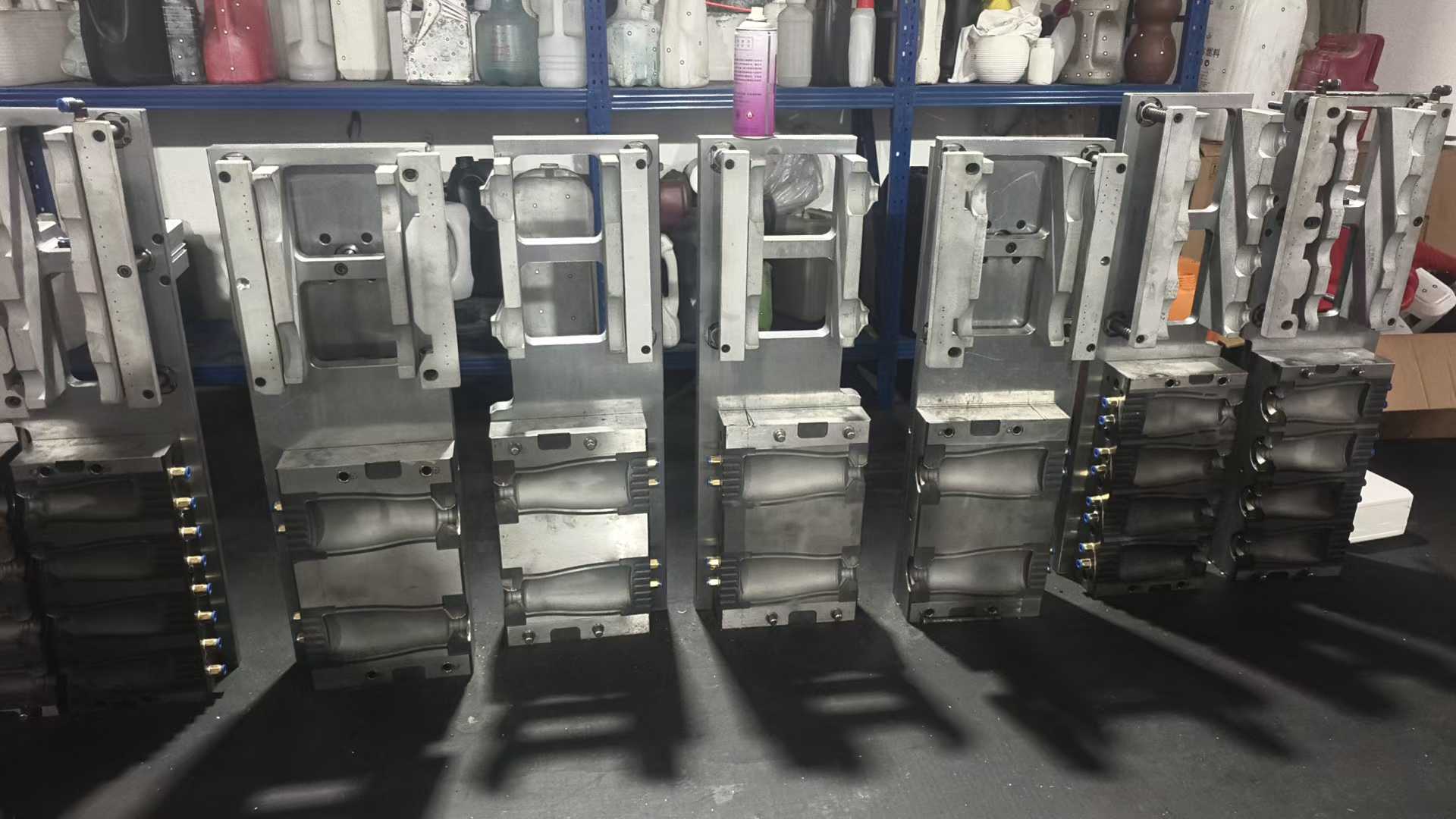
Hollow Extrusion Mold Manufacturers for Blow Molding Machines – A Complete Guide
Introduction
Hollow extrusion molds are critical components in blow molding machines, used to produce plastic bottles, containers, and industrial hollow products. Choosing the right hollow extrusion mold manufacturer ensures high-quality production, efficiency, and durability.
This guide covers top manufacturers, key selection criteria, and industry trends for blow molding machine molds.
1. What Are Hollow Extrusion Molds?
Hollow extrusion molds are specialized blow molding dies that shape molten plastic into hollow products. They are used in:
Extrusion Blow Molding (EBM) – For large containers (e.g., drums, fuel tanks).
Injection Blow Molding (IBM) – For precision bottles (e.g., medical, cosmetic).
Stretch Blow Molding (SBM) – For PET bottles (e.g., beverage, detergent).
Key Features:
✔ High wear resistance (chrome-plated steel, aluminum alloys)
✔ Precision cooling channels for faster cycle times
✔ Customizable cavity designs
2. Top Hollow Extrusion Mold Manufacturers & Suppliers
A. Global Manufacturers
Jomar Corporation (USA) – Specializes in high-performance extrusion blow molds for industrial packaging.
Techne UK (UK) – Leading supplier of custom blow molding dies for automotive and packaging.
Zhongde Plastic Machinery (China) – Major exporter of cost-effective EBM and IBM molds.
B. Asian Suppliers (China & India)
Haitian International – Produces high-precision PET blow molds.
R.D. Industries (India) – Known for durable extrusion blow molding dies.
C. European Precision Mold Makers
Kautex Maschinenbau (Germany) – Advanced multi-layer extrusion molds for automotive fuel tanks.
SACMI (Italy) – Specializes in beverage bottle molds for SBM machines.
3. How to Choose the Right Manufacturer?
A. Material & Durability
Hardened steel – Best for long production runs.
Aluminum alloys – Lightweight, ideal for prototyping.
B. Cooling Efficiency
Optimized cooling channels reduce cycle time.
C. Customization & Tolerance
CAD/CAM-designed molds for complex shapes.
±0.05mm precision for consistent output.
D. After-Sales Support
Look for maintenance, repair, and mold optimization services.
4. Industry Trends in Blow Molding Molds
✅ Multi-Layer Molds – For barrier-enhanced packaging (e.g., UV-resistant, oxygen-blocking).
✅ Quick-Change Mold Systems – Reduces downtime in production.
✅ AI & IoT Integration – Smart molds with real-time monitoring.
Conclusion
Selecting the right hollow extrusion mold manufacturer is crucial for efficient blow molding production. Consider material quality, cooling efficiency, and customization when choosing a supplier.