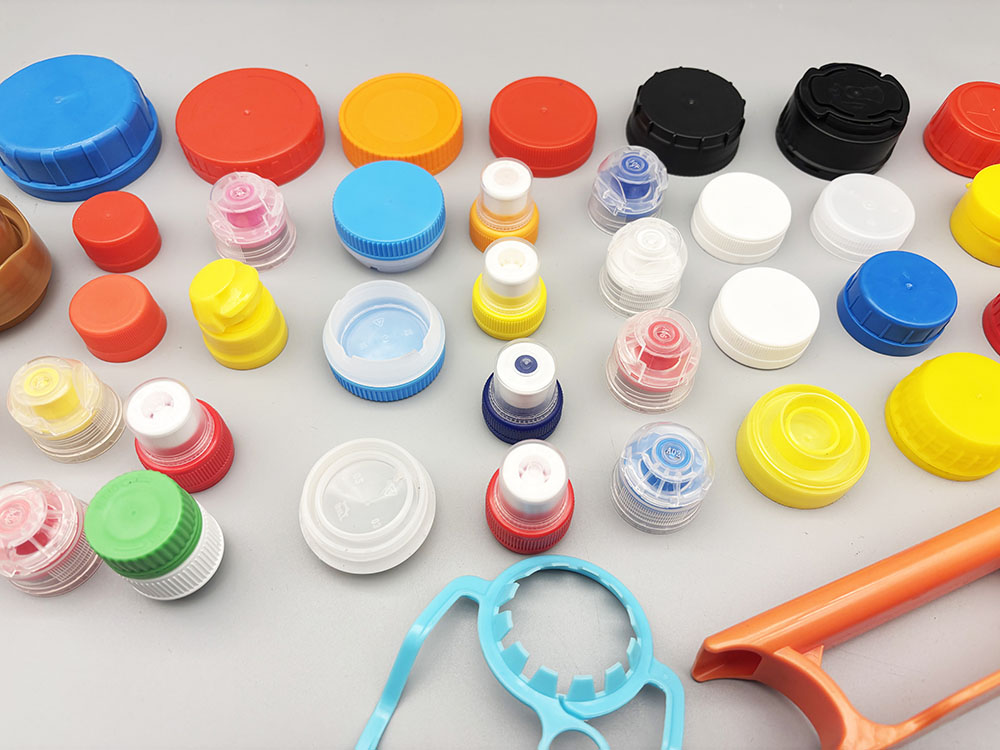
The manufacturing process of plastic bottle cap molds usually includes the following steps:
The manufacturing process of plastic bottle cap molds usually includes the following steps:
The manufacturing of plastic bottle cap molds is a complex and highly sophisticated process involving design, material selection, processing technology, quality control, etc. The following is a detailed analysis of bottle cap molds, covering key technologies and core points in practical applications:
1. Design and Engineering Analysis
Requirement Analysis: Clarify the function, size and material requirements of the bottle cap.
3D Modeling: Use CAD software to create a three-dimensional model of the mold.
Engineering Analysis: Perform mold flow and structural analysis through CAE software to optimize the design plan.
2. Material Selection
Mold Steel: Select suitable steel according to production needs, such as P20, H13, etc.
Heat Treatment: Heat treat the steel to improve hardness and wear resistance.
3. Processing and Manufacturing
CNC Processing: Use CNC machine tools to process the core and cavity of the mold.
EDM Processing: Use electric spark to process complex shapes and details.
Grinding and Polishing: Ensure the mold surface is smooth and reduce demolding resistance.
4. Assembly and Debugging
Assembly: Assemble the components into a complete mold.
Debugging: Test the mold on the injection molding machine and adjust the parameters to ensure product quality.
5. Surface Treatment
Coating: Add wear-resistant or anti-corrosion coating as needed.
Polishing: further improve the surface finish.
6. Quality inspection
Dimension inspection: use tools such as three-coordinate measuring machines to check dimensional accuracy.
Functional testing: ensure that the mold can stably produce qualified products.
7. Delivery and maintenance
Delivery: deliver the mold to the customer and install and debug.
Maintenance: regular maintenance to extend the life of the mold.
1. Core design requirements of bottle cap mold
Function matching
Sealing: It is necessary to ensure that the sealing structure of the bottle cap and the bottle mouth (such as internal thread, gasket groove) is accurately matched.
Anti-counterfeiting design: For example, the demoulding structure of the broken anti-counterfeiting ring (anti-theft ring) requires special design.
Opening convenience: For example, the mechanical properties of the screw cap, flip cap or pump head need to be realized through the mold structure.
Structural complexity
Multi-cavity mold design: In order to improve production efficiency, the "one-out multi-cavity" layout (such as 1-out 32 cavities) is often adopted.
Slider and inclined top mechanism: used for demoulding complex structures (such as internal threads, undercuts).
Hot runner system: Reduce waste and improve injection molding uniformity, suitable for high-precision bottle cap production.
Material adaptability
Plastic characteristics: Adjust the shrinkage rate and cooling system of the mold according to the bottle cap material (such as PP, PE, PET).
Wear resistance: Frequent demoulding parts (such as threaded cores) require high-hardness steel or surface coating (such as DLC coating).