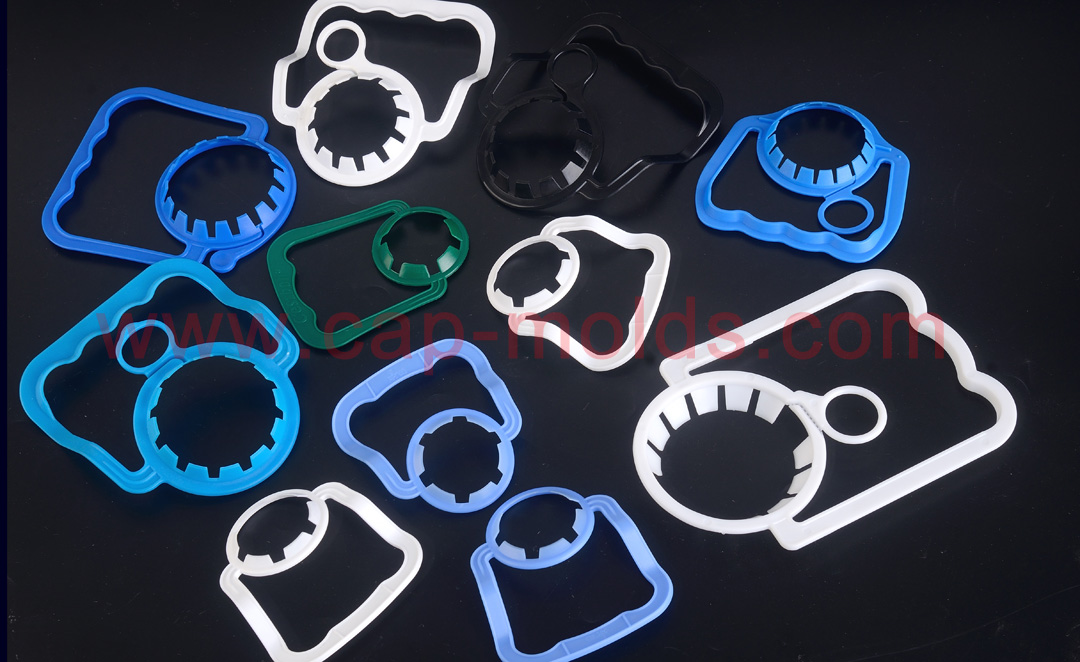
Plastic Injection Pet Preform and water bottle cap & handle mould mold
Shuanghao Mold company not only offer you Engineering service for plastic injection pet preform and water bottle cap & handle moulds manufacturing, but also offer you the cap and preform mold high speed molding solutions.
Product Name | Plastic handle mould |
Core &Cavity Steel | 2316#steel, S136, H13, 718, SKD61, P20, S50C, 45#steel, 4Cr13, |
3Cr13, BeCu or based on customer's requirement. | |
Mould base & Standard Component | DME,HASCO,MISUMI,LKM,Self-made etc. |
Steel hardness: | HRC30-35 for base material. |
HRC45-48 for core and cavity material. | |
HRC60-62 for special parts material | |
Plastic material | PP,,PE,HDPE etc. |
Cavity Number | 1*4, 1*6, 1*8,1*12, 1*16, 1*24, |
Injection System | Pin gate, Submarine gate, Valve gate etc |
Ejector System | stripper plate, ejector sleeve, ejector pin |
Cycle Time | Based on cap design |
Tooling lead time | 30-60 Days |
Mould life | At least 1.5million Shots |
Handle Mold Feature |
1. Adopt imported steel P20, Germany 2316, S136 etc. |
2. Each cavity and core have independent cooling system, with independent parts for replacement |
3. Rational mold design to extend mold life and get high production efficiency. |
4. Mirror hand polishing and mold plates chroming to create added-value. |
5. Precision Machining to ensure high production efficiency & fine parting line effect. |
6. Skilled Language in communication and experienced in international standard. |
7. Hot runner system: China advanced brand or imported hot runner system brand. |
Each cavity has independent temperature control and heater system. |
Plastic handle mould | |
1.R&D | We support customer R&D. Make the files or improve the design if you needed. |
2.Quotation Making | Mould Quotation will be finished in 1 day according to information we get. |
3.Negotiation | The quality, price, material, delivery time, payment item, etc. |
4.Mould Design | 1-2days for product 3D/2D drawing design as per customer's design or our company's design. Then in further make the mould 2D/3D design. |
5.Mould | 1. confirm the proucts and the mold design |
2. Mould material prepare | |
3. Rough machining(heat treatment on mold base and pre-harden on mold) | |
4. CNC/ Vacuum Hardening on mold main spare parts | |
5. finishing machining( JDPAINT, DEM.etc) | |
6. Dimension inspection | |
7. Ejector& runner& cooling & other device process | |
8. Assemble mold | |
6.Mould Testing | When moulds are finished, we will test the mould and we will send samples for consumer reference. |
7. Sample confirmation | If the first sample is not satisfied by customer when it is come out. We modify the mould and until meet customer’s satisfaction. |
8.Delivery | Delivery goods by sea or by air, according to customer’s requirement. |